Understanding Plastic Injection Tools: A Comprehensive Guide for Metal Fabricators
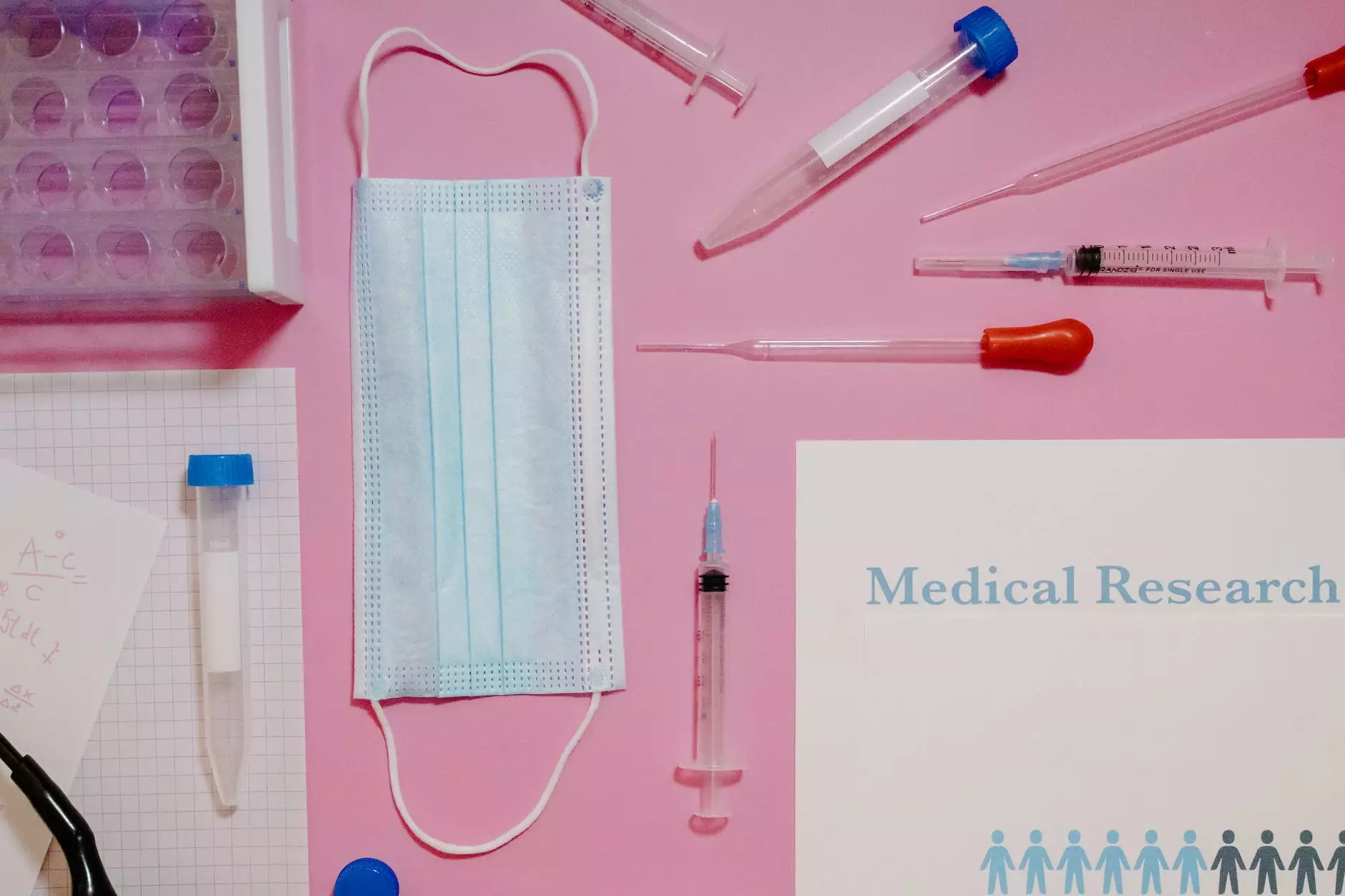
In the ever-evolving landscape of manufacturing and fabrication, plastic injection tools play a critical role. These tools are essential for shaping and molding plastics used in a wide range of applications, making them invaluable for metal fabricators looking to diversify their offerings and improve efficiencies. This article explores the significance, types, applications, and advancements of plastic injection tools within the metal fabrication industry.
The Importance of Plastic Injection Tools in Fabrication
Plastic injection molding is a highly efficient process that allows manufacturers to create complex parts quickly and accurately. For metal fabricators, investing in plastic injection tools can lead to numerous benefits:
- Cost-effectiveness: High-volume production can significantly reduce costs per unit.
- Precision: Advanced technologies ensure high levels of precision and repeatability.
- Material Versatility: A wide range of plastics can be used, offering flexibility in design and use.
- Reduced Waste: The process is designed to minimize scrap material, optimizing resource use.
Types of Plastic Injection Tools
Understanding the different types of plastic injection tools available is crucial for metal fabricators. Here are the primary types:
1. Injection Molding Machines
These machines are at the heart of the injection molding process. They come in various sizes and capabilities, designed to meet specific production needs:
- Hydraulic Injection Molding Machines: These are traditional and are known for their strong clamping force.
- Electric Injection Molding Machines: These offer higher precision and lower energy consumption.
- Hybrid Injection Molding Machines: Combining hydraulic and electric technologies, these machines provide versatility and efficiency.
2. Molds and Tooling
The molds used in plastic injection are critical to the success of the process. They come in various designs based on the part specifications:
- Single-Cavity Molds: Used for lower volume production, creating one part per cycle.
- Multi-Cavity Molds: Increase productivity by allowing multiple parts to be produced in a single cycle.
- Family Molds: Designed to produce different parts in one cycle, ideal for related components.
Applications of Plastic Injection Tools in Metal Fabrication
The use of plastic injection tools extends across various sectors of metal fabrication. Here are notable applications:
Automotive Industry
In the automotive sector, these tools create components that require high durability and precision, such as:
- Dashboard components
- Interior fittings
- Casings for electrical systems
Consumer Electronics
Plastic injection molding is vital for producing lightweight, durable casing and various electronic components, such as:
- Smartphone housings
- Television frames
- Component brackets
Medical Devices
The medical sector benefits from plastic injection tools in producing:
- Surgical instruments
- Drug delivery systems
- Disposable medical supplies
Advancements in Plastic Injection Tools
The field of plastic injection molding is continually advancing, leading to new technologies and methodologies. Some of the latest advancements include:
Smart Molding Technology
Utilizing IoT and AI, smart molding technology allows for real-time monitoring and adjustments, enhancing production efficiency and reducing downtime.
Advanced Materials
New formulations of plastics, including bio-based and recycled materials, provide manufacturers with more options, promoting sustainability.
3D Printing Integration
Combining 3D printing with injection molding allows for rapid prototyping, lowering the barrier for product design iterations and speed to market.
Choosing the Right Plastic Injection Tools
For metal fabricators, selecting the right plastic injection tools is paramount for ensuring high-quality production. Consider the following factors:
- Production Volume: Determine whether you need a high-output machine for mass production or a more flexible setup for smaller runs.
- Complexity of Parts: Choose molds that can handle the intricacies of the parts you intend to produce.
- Material Compatibility: Ensure that the tools and machines can accommodate the specific types of plastics required for your projects.
- Budget: Balance initial investment with potential long-term savings through efficiency and lower operational costs.
Conclusion
In conclusion, plastic injection tools are an essential asset for metal fabricators looking to enhance their operations and offer new products. Understanding the different types of tools available, their applications, and the latest advancements in technology is crucial for staying competitive in the industrial landscape. By investing in the right tools and continuously adapting to newer technologies, metal fabricators can unlock significant value and drive growth in their businesses.
At Deep Mould, we specialize in providing high-quality plastic injection tools and molding solutions that cater to the unique needs of each of our partners in metal fabrication. Contact us to learn how we can help you revolutionize your production process today.